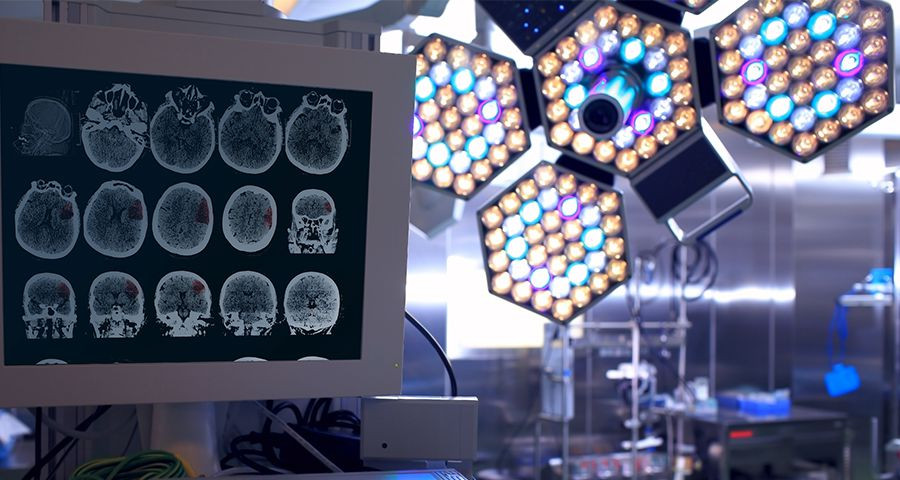
Medical power supplies standard challenges
The general standard IEC 60601 is the accepted standard for medical equipment, especially for medical electrical equipment and general requirements for basic patient safety.
The standard 60601 is a widely accepted benchmark series for medical electrical equipment and compliance with IEC60601 has become a de-facto requirement for the commercialization of electrical medical equipment in many countries
The 3rd edition of this medical safety standard was first published by the IEC in 2005 (IEC60601-1:2005) and was adopted by the European Union in 2006 and published as EN60601-1:2006. The USA version was also published in 2006, but unlike 2nd edition, not by UL. It is published by the American Association for Medical Instrumentation (AAMI) and appears as ANSI/AAMI ES60601-1:2006. Canada published the standard in 2008 as CAN/CSA60601:2008.
Engineers need to be acutely aware that when using these standards, there are a number of key dates specified for the implementation of the 3rd edition, and that these vary by region.
In Europe, as of the 1st June 2012 the 2nd edition (EN60601-1/A2:1995) will be withdrawn, called the cessation date, and all products will need to be certified to the 3rd edition, EN60601-1:2006. This includes both new products introduced to the market and products already on sale.
The situation is rather different in the United States
The cessation date for 2nd edition (UL60601-1:2003 1st ed) is 30June 2013 but, unlike the EU, the FDA only requires that new products brought to market after this date will need to be 3rd edition certified (ANSI/AAMI ES60601-1:2005). In Canada the cessation date for 2nd edition (CAN/CSA C22.2 No. 601.1) is 1 June 2012, but again the 3rd edition (CSA‐C22.2 NO. 60601‐1:08) is only needed for products new to the market after this date.
Another complicating factor for designers is that the particular standards that are part of the 60601 family. These are commonly referred to as "part 2's" and will have the standard number 60601-2-xx, such as IEC60601-2-46, particular requirements for the safety of operating tables. Where these are applicable the equipment needs to be certified to these standards and therefore the date for 3rd edition adaption will be dictated by the date that the 2nd edition part 2 is withdrawn.
This could be before the main date or after it. Some countries are, to date, not adopting 3rd edition. This means that equipment will need to be certified to IEC60601-1/A2:1995 2nd edition for those regions, because after 1st June 2012 EN60601-1 2nd edition will be withdrawn and UL60601-1 will be withdrawn in June 2013.
Certifying all power supplies
XP Power has taken the decision to certify all power supplies to 3rd edition (with 2 x Means Of Patient Protection on the majority of power supply), but to also test against 2nd edition. The rationale here is that following 2 x MOPP in 3rd edition is equivalent to the 2nd edition in terms of separation distance, insulation schemes and dielectric strength requirements. This means that the OEM will be able to claim the safety of the power supply is at least as good as the current standard (2nd edition) and will still maintain the equipment 2nd edition approval, even with a 3rd edition (2 x MOPP) approved PSU.
One of the most significant changes that the 3rd edition introduces is that equipment manufacturers must now follow a formal risk management procedure that follows the ISO 14971 model, which effectively means compliance with a process standard as well as the fundamental product standard.
While the 2nd edition simply addressed basic safety issues to ensure freedom from any electrical, mechanical, radiation, and thermal hazards, it did not require devices to remain functional in that fail-safe was adequate, and compliance with test criteria relied upon a pass/fail result that did not take into account the essential performance of the device-under-test. Recognizing these limitations, the 3rd edition introduces specifications for "essential performance" that require that equipment will continue to function as its designers intended throughout the test process.
Within the electrical safety arena, the standard continues to require that equipment implements two Means of Protection (MOP) such that if a failure occurs within one area, a second mechanism safeguards the operator and/or the patient against any electric shock hazard. Figure 1 models the insulation diagram that applies to the main circuit blocks in a notional medical device, and shows the two isolation barriers that provide the two means of protection that must be present within a device that may come into contact with a patient.
Figure 1: IEC60601-1 3rd edition demands that two means of protection (MOPs), or isolation barriers exist where patients may come into contact with equipment.
Key caption:
AP = applied part
B(xx) Basic insulation (working voltage)
D = Double insulation
LP = Live part
MP = Mains part
OP = Operational insulation
R = Reinforced insulation (working voltage)
The standard allows for three defensive approaches that may be used in various combinations: safety insulation, protective earth, and protection impedance. It is therefore essential to determine several key factors from the outset of the equipment design process, including its insulation class and whether it will rely upon a protective earth connection.
These considerations extend to the “applied part”, if present, that is deliberately attached to the patient. Such applied parts are separately classified as to the level of electric shock protection that they provide.
Significantly for power supplies, the 3rd edition distinguishes between protecting the equipment's operator and the patient within its Means of Operator Protection (MOOP) and Means of Patient Protection (MOPP) categories.
This distinction can result in quite different safety insulation and isolation requirements for circuits that operators and patients may come into contact with. Specifically, anything that falls within the remit of operator protection only has to meet the clearance and creepage requirements that IEC/EN 60950 specifies for general-purpose information and technology equipment.
By contrast, circuitry that falls within the realm of patient protection must meet the far more exacting requirements that the 2nd edition of IEC 60601-1 introduced. As to who determines whether it is MOOP or MOPP is up to the manufacturer and they will need to record this in the risk management file.
Making the correct choice
In choosing a power supply with only MOOP, one would have to ensure other isolation schemes are in place between the output and the patient if the equipment is to come in contact with the patient. It complicates the design and increases cost, even though the cost of the MOOP power supply might be less than that of an MOPP power supply.
No matter whether MOOP or MOPP is chosen the standard still requires that the leakage current requirements are met. For the power supply this means 300µA for the USA and 500µA for the EU.
As most people know, if one has to modify an ITE power supply to achieve these leakage current levels, then the emissions will be impacted and additional filtering will probably need to be added to the equipment.
From this standpoint XP Power believes that the power supply for a medical device should provide the highest degree of protection and reduce the risk of a shock hazard.Therefore the company has taken the decision to make its power supplies to have 2 x MOPP from input the output (mains to low voltage dc). This gives customer flexibility and assurance that they have minimized the risk of a shock hazard.
A major component to the 3rd edition is for a Risk Management Process to be included as part of the submittal to the certified body which will undertake the product certification. While risk management is not a new concept to device manufacturers, it is new for the power supply manufacturers.
Under 2nd edition, the certified body would test against pass/fail criteria, which was very specific. It is true that these same pass/fail criteria exist under 3rd edition but it is also required that risk management is included. The IEC recently published a guidance note for power supply manufacturers specifying that 3rd edition could be gained without risk management, but that the device manufacturer would have to cover this during their submittal.
While it may appear this provides a low cost route for PSU manufacturers to gain certification, it merely pushes the cost back to the device manufacturer and ultimately the device manufacturer will require the PSU manufacturer to provide risk analysis, Failure Mode Effects Analysis (FMEA) etc. If the power supply manufacturer does not have this prepared then there could be a delay in obtaining this valuable information.
The policy at XP Power is to submit a risk management process with all submittals and to make this available to customers where necessary. XP customers can now be assured that the power supply is simply a "black box" and only consider the implications of output failing etc.
The internal analysis is fully completed by XP Power. In order to achieve this, XP embraced ISO14971 such that risk management is now part of the design process. For the production aspects of certification, XP now has its factory approved to ISO13485, which is the quality management system for medical devices.